現代社会において、半導体は身の周りのあらゆる製品に使われていると言っても過言ではないぐらい重要なものとなっています。「産業の米」と言われていることはご承知のとおりです。
熊本に進出するTSMC(JASM)は、半導体の事業形態の中では、製造に特化した事業である「ファウンドリー」というカテゴリーに分類されます。ファウンドリーについては以下の記事をご参考に。
実は、このファウンドリーという製造工程だけでも、ものすごく多くの工程が存在し、かつ多種多様で高度な技術を要します。
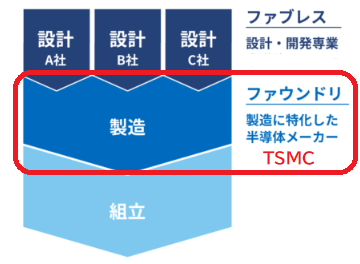
半導体製造工程は、主に設計、前工程と後工程に分かれます。
前工程は、ウェーハー検査までの工程のことであり、後工程はウェーハー検査で良品として判定されたチップを取り出してから出荷までの工程をいいます。
では、これらの工程について、順を追って説明します。
設計
回路・パターン設計
まず、半導体チップ上にどのような回路を配置するのか設計し、その回路が正しいかシミュレーションを繰り返して効率的なパターン設計を行います。
当たり前ですが、用途によって必要な機能が異なるため、設計する回路は都度違うものとなります。
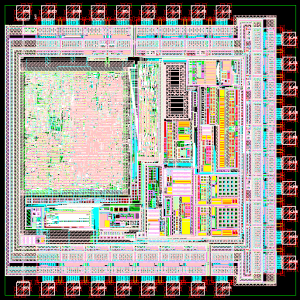
前工程
フォトマスク作成
コンピュータを使い透明なガラス板の表面に、設計された回路パターンを描きます。
これが、ウェーハに回路を転写するための原版(マスタ)となります。
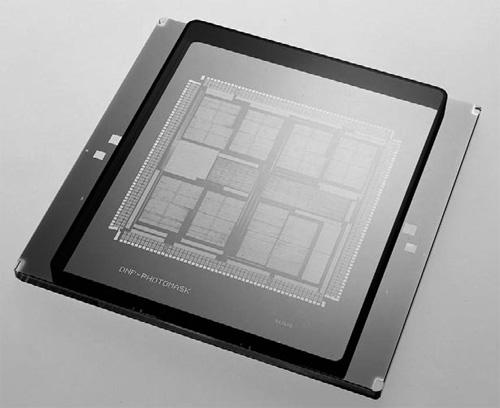
シリコンの精製
初めに高純度のシリコンを製造します。
通常は石英を原料とし、冶金プロセスを使用して不純物を取り除き、高純度のシリコンを得ます。
シリコンインゴットの成長
高純度のシリコンを溶融させ、結晶成長を行います。
これによってシリコンインゴットが形成されます。
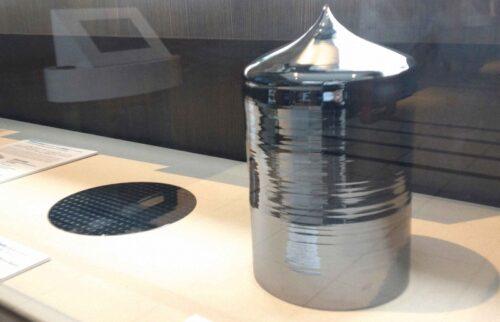
シリコンウェーハーの切削
シリコンインゴットを薄い円盤状に切削します。
これによって複数のウェーハーが得られます。
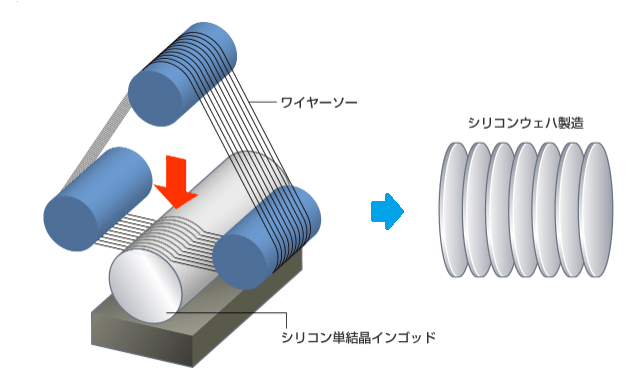
ウェーハーの平坦化
ウェーハーの表面を平坦にするためのプロセスを行います。
これによってウェーハーの厚さが均一になり、後続の工程に影響を与えないようにします。
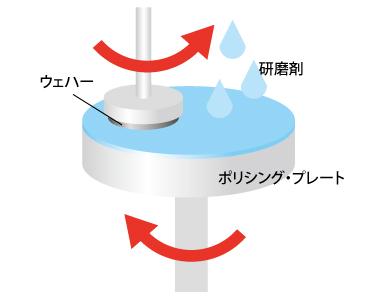
ウェーハーの洗浄
ウェーハーの表面に付着した不純物や汚れを取り除くために洗浄プロセスを行います。
ウェーハーのクリーンな表面は、デバイスの品質と性能に影響を与えます。
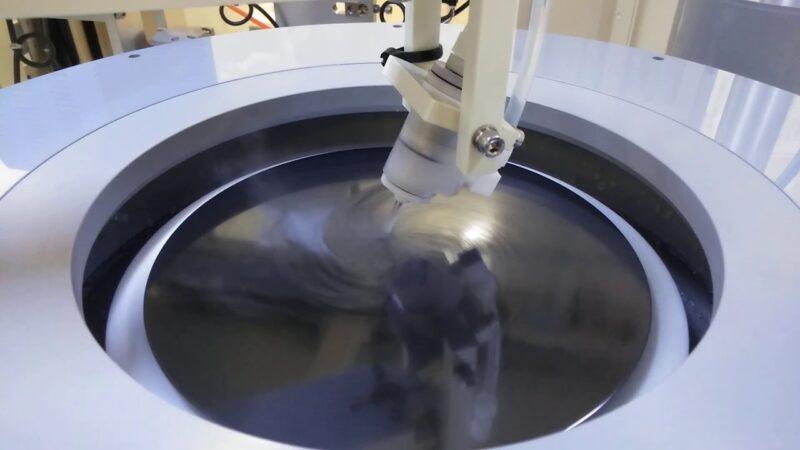
ウェーハーのドープ
シリコンウェーハ表面にホウ素やリン、ヒ素などをしみこませ、シリコンウェーハ中にトランジスタやダイオードなどの素子を形成させます。
これによって、半導体デバイスの性能が制御されます。
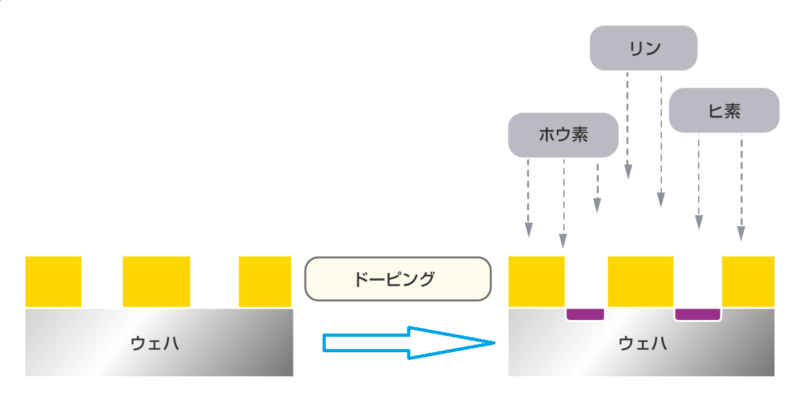
ウェーハー表面の酸化
ウェーハー表面に酸素を供給して酸化膜を形成するプロセスです。
これによってウェーハー表面が保護され、絶縁体やゲート絶縁体が形成されます。
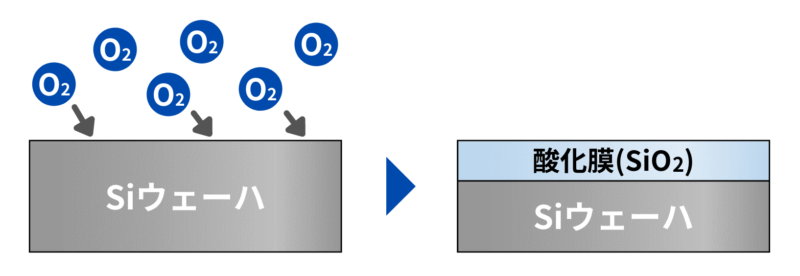
フォトリソグラフィ
ウェーハー上に微細なパターンを転写するためのマスクを使用し、光学的な露光と薬品処理を行います。
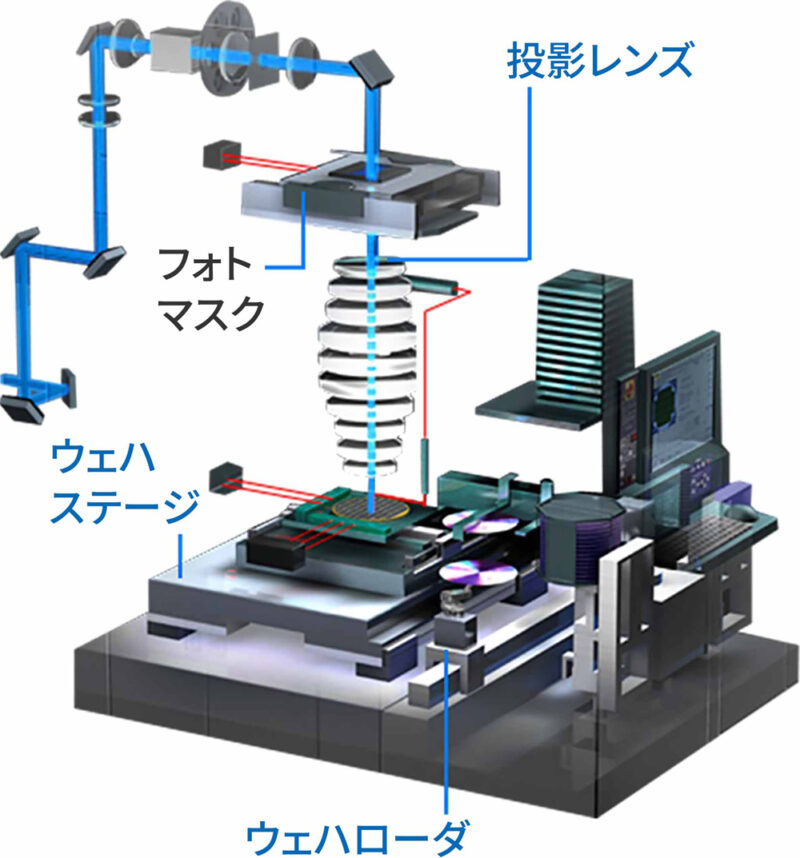
エッチング
フォトリソグラフィで形成されたパターンを基に不要な材料を削除します。
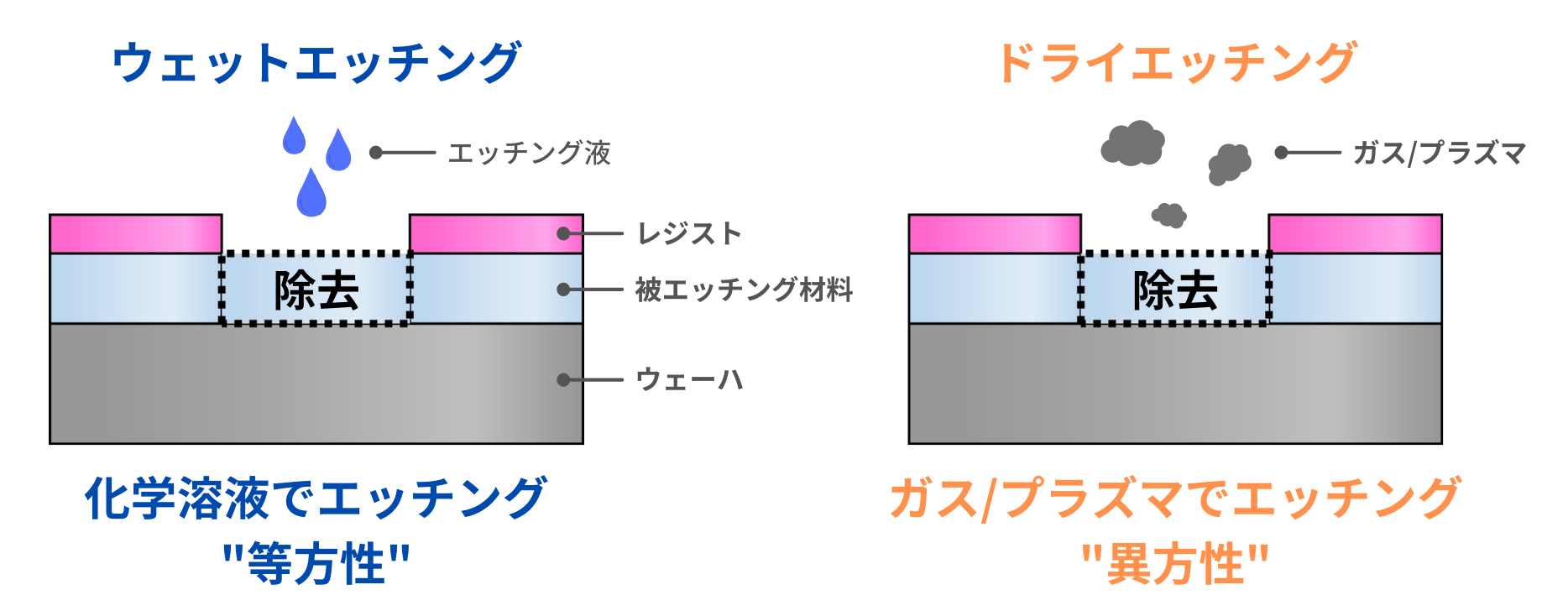
- 古くから伝わる腐食作用を利用して行う表面加工の技術のことです。銅などをはじめとした金属が加工の対象で、その表面の微細加工に用いられます。
- 一般的には、最初に加工を行う金属の表面の残したい部分にのみ防食処理を行い、硝酸などの腐食剤で不要な部分を溶解侵食して除去するのが基本的な方法です。
- 半導体製造におけるエッチングには、「ウェットエッチング」と「ドライエッチング」の2種類があります。
- 「ウェットエッチング」は、酸やアルカリなどの薬液で金属を溶解する方法です。
- 「ドライエッチング」は、ガスをプラズマ化してイオンで金属を除去する加工方法です。この方法は電極の間で反応が加速したガスを金属の表面にぶつけて膜を削ることで加工します。
- 「ドライエッチング」は周囲を汚染しにくく精度が高いですが、「ウェットエッチング」と比較すると費用が高くつくというデメリットも存在します。
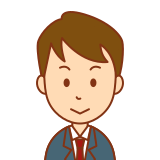
薬剤を使用する「ウェットエッチング」は、「ドライエッチング」より危険性が高そうですけど有名なファウンドリーでも使用していますか?
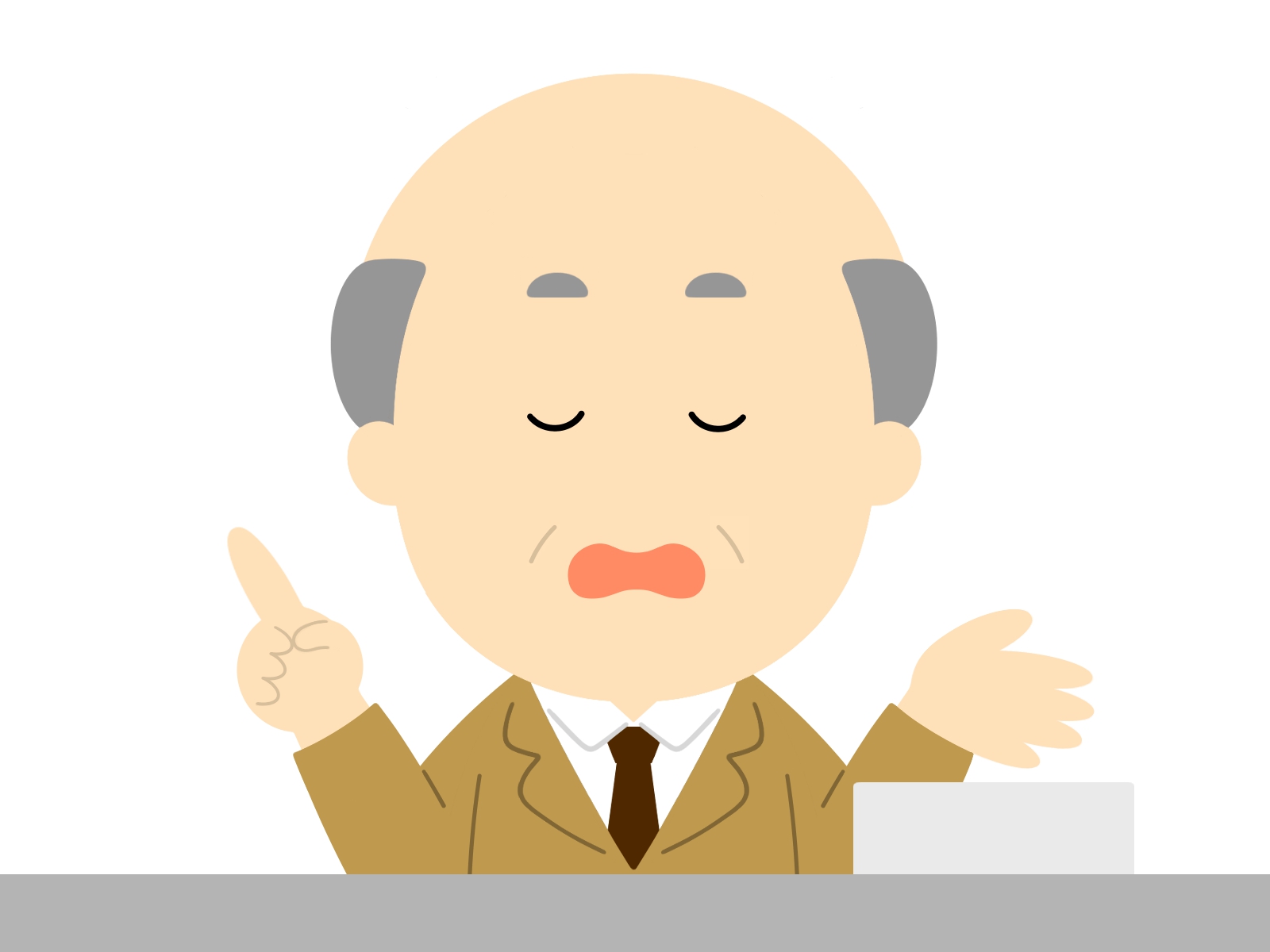
いい質問ですね。近年ではドライエッチングが主流になっています。なぜなら、等方性が特長のウェットエッチングは、加工精度が低いため微細加工には不向きです。
CVD
ウェーハー上に薄膜を成長させるためのガスを化学反応させるプロセスを行います。
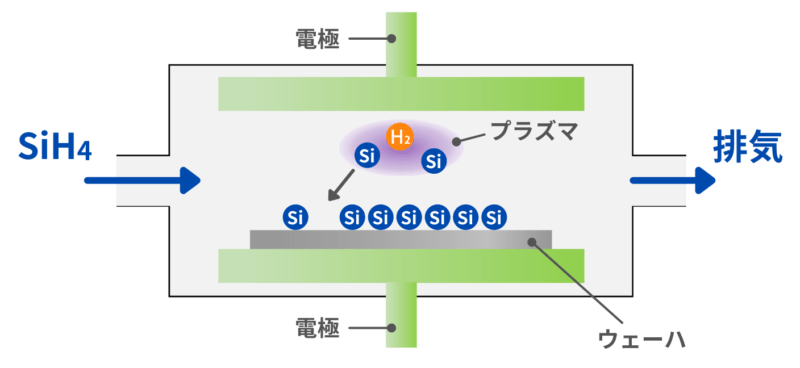
- プラズマCVDとはプラズマ励起化学気相成膜(Plasma Enhanced Chemical Vapor Deposition:PECVD)とも呼ばれます。シリコン窒化膜(SiN)やシリコン酸化膜(SiO2)の成膜に使用されます。
- ウェーハーの上に供給した原料ガスを直流(DC)電流や高周波(RF)電流、マイクロ波などによってプラズマ化して中性励起粒子を活性化させます。基板上で化学反応を発生させて生成された物質を堆積させて薄膜を形成する方法です。
イオン注入
イオンビームを用いて特定の元素をウェーハー上に導入し、電気的特性を調整します。
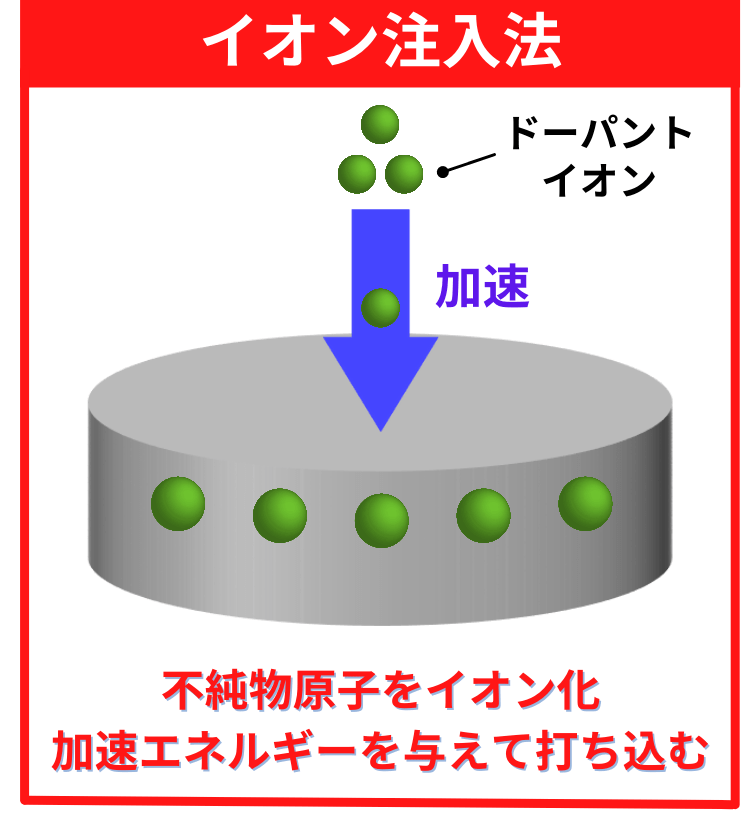
イオン注入は「不純物をイオン化して高電圧で加速することでウェーハに注入する方法」です。
デバイスの作成にはp型領域とn型領域を詳細に作り分ける必要があるため、不純物の精密な導入が非常に重要になります。
電極形成
電極配線用の金属をウェーハに埋め込むことで、チップ内部と外部を電気的に接続するための通り道を作ります。
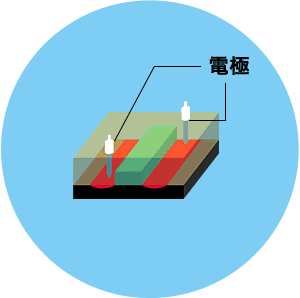
ウェーハー検査
ウェーハーに形成された数百個のチップのひとつひとつに対して、プローブと呼ばれる針を接触させ電気的に問題がないかを検査します。
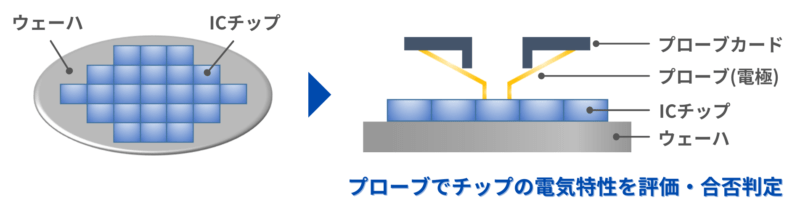
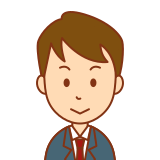
1枚のウェーハーにはたくさんのICチップができるんだね。これら全てのICチップを検査して不良品を除いたICチップだけが後工程に渡されるということですね。
後工程
ダイシング
ウェーハーをダイヤモンドブレードで切断して、ひとつひとつのチップに分離させます。
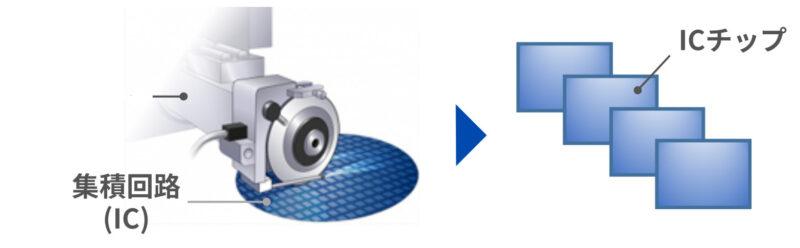
ワイヤーボンディング
リードフレームと呼ばれる金属の枠にチップを固定し、金線で接続します。これにより、チップとの配線が可能になります。
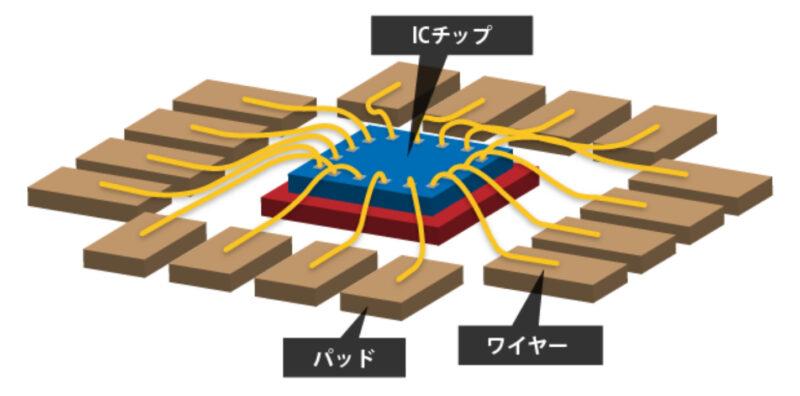
モールディング
チップを傷や衝撃から保護するため樹脂でパッケージします。
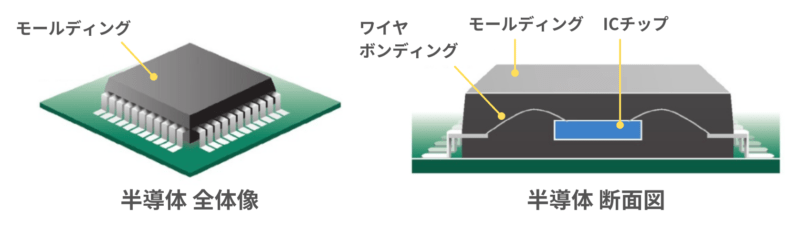
最終テスト
温度や電圧の試験、電気的特性試験、外観構造検査など、異常がないか何重もの試験を行い、不良品を取り除きます。
出荷
品質が確認されたデバイスは、顧客やエンドユーザーに出荷されます。
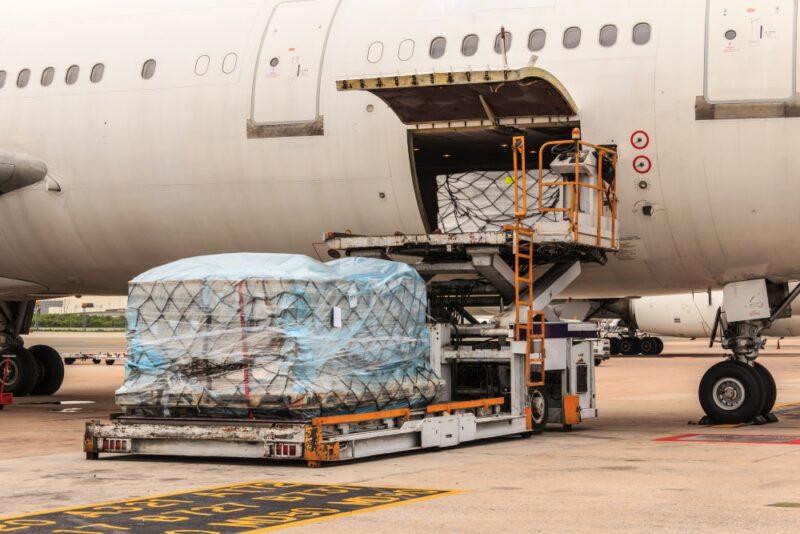
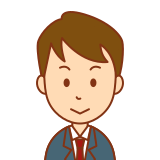
半導体は製品サイズが極端に小さいから空輸で十分ですね。
まとめ
このように半導体製造工程は、細かい工程も含むと前工程と後工程を合わせて数百工程から成り立っていると言われています。
日本の半導体は大きくシェアを落としてしまいましたが、それは半導体集積回路(デジタル)のことであり、半導体材料(ウェーハーでは日本の2社で世界の60%以上のシェア)や、半導体製造装置(世界トップ10の4社は日本)においては、まだまだ健在です。
実は、工程ごとに細かく見ていくと意外に知られていない事実が見えてきます。
- フォトマスク市場(2023年8月):凸版印刷・大日本印刷で世界シェア約5割
- シリコンウエハ売上高ベンダ国籍別シェア(2021年):国内企業上位2社でシェア53%
- 半導体製造装置世界ランク(2022年):上位10社中4社が日本企業
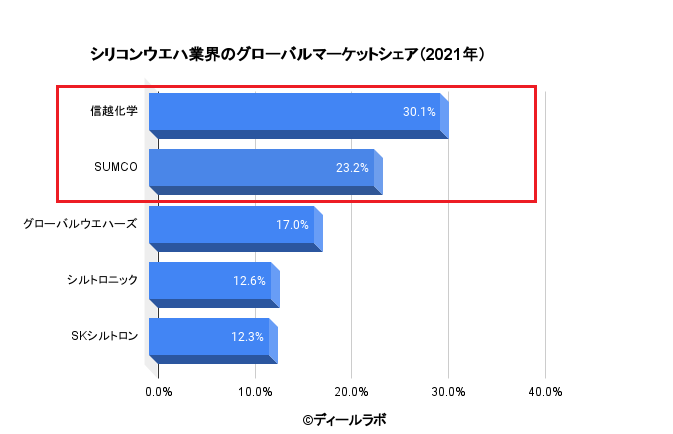
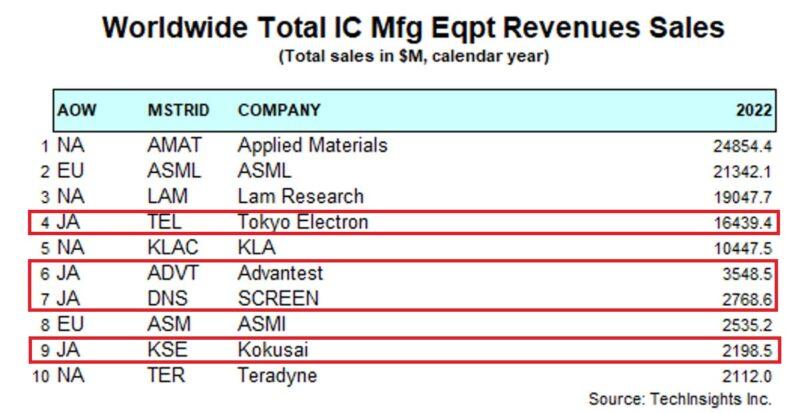
このように、ハイテクノロジーの集大成ともいえる半導体製造において、日本企業の貢献度はまだまだ非常に大きいことがわかります。
なぜ、半導体集積回路(デジタル)だけは大きくシェアを落とすことになったのでしょう?
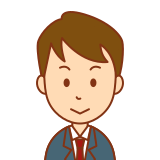
なぜなの?
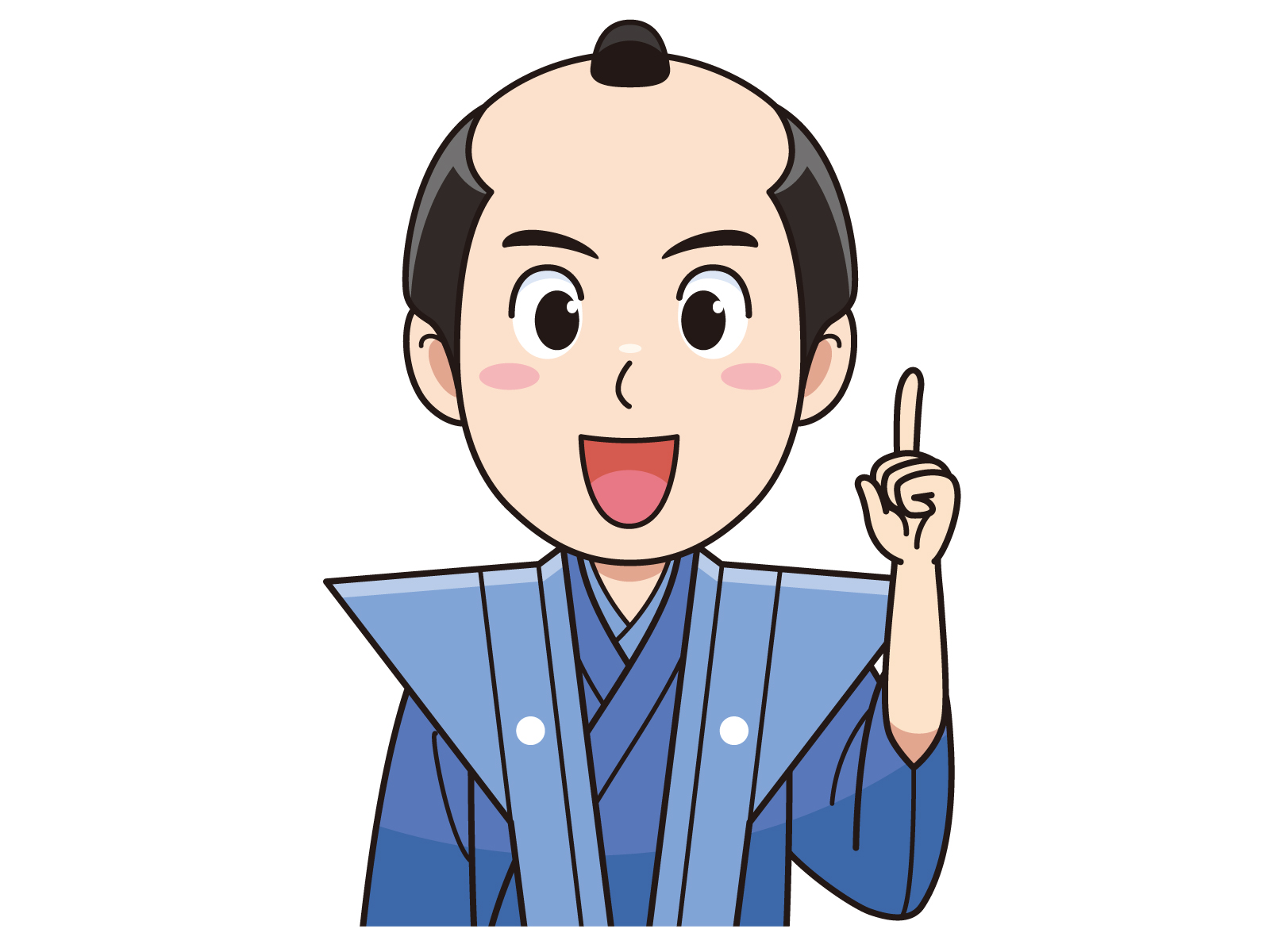
歴史(学校では教えない)を学べば答えがわかります。💦
次回は、国内企業と関りが深い工程について、さらに深掘りする予定です。
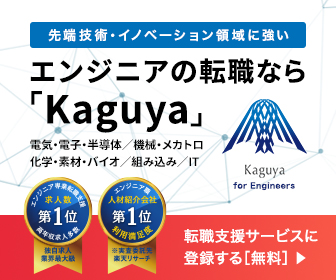